Ambiguity of Inside-Out – CO Architects at the Boston Valley Terra Cotta Architectural Ceramics Workshop
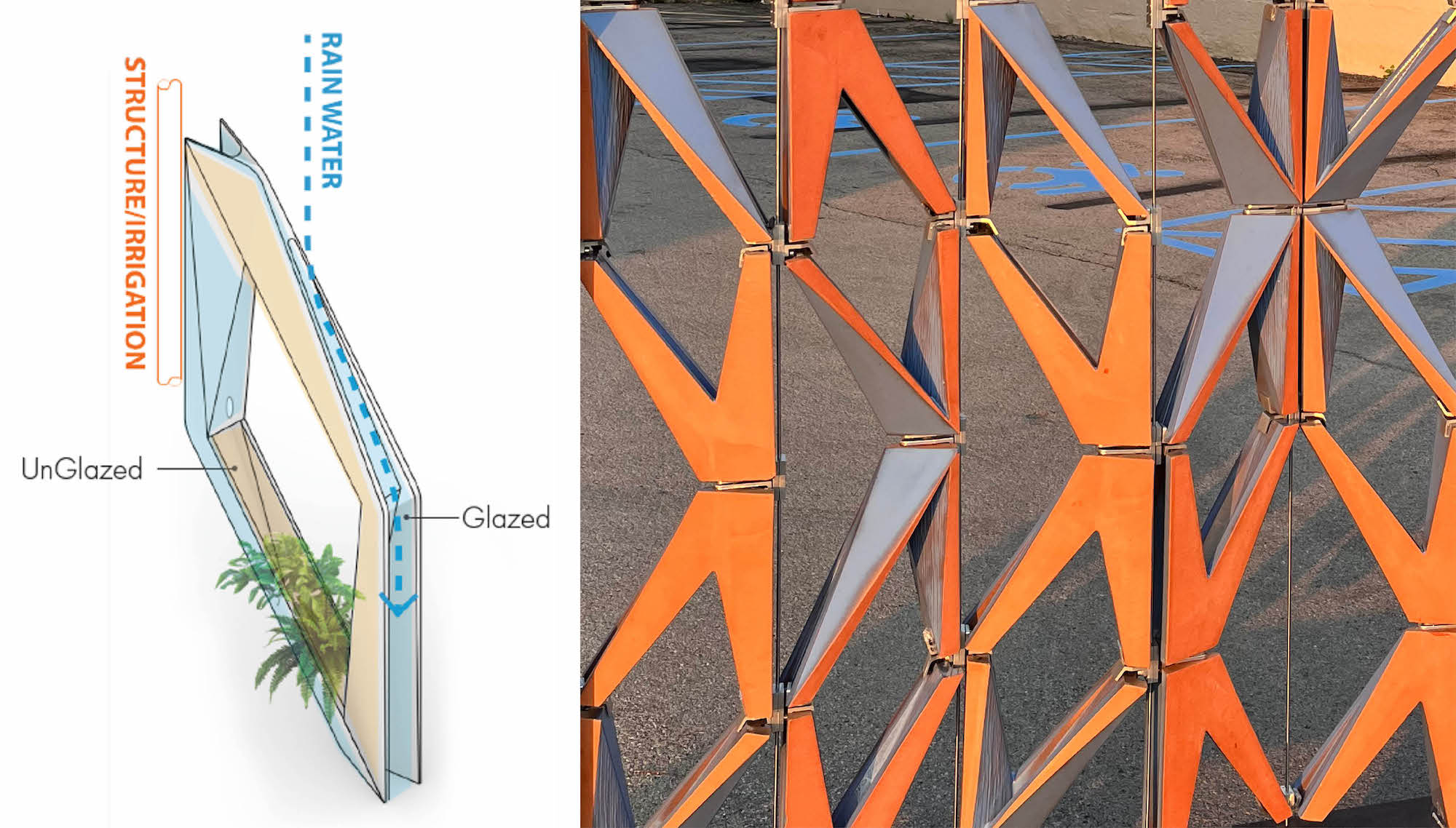
By Kaiwen Ku and Chun-Li Chen (Julie)
Earlier this year, CO Architects was invited to participate in the annual Architectural Ceramics Assemblies Workshop hosted by Boston Valley Terra Cotta. To determine who would attend the workshop, our office held an in-house design competition. Four teams presented their designs to the office in March. Kaiwen Ku and Chun-Li (Julie) Chen’s design titled Ambiguity of Inside-Out was the winner!
Kaiwen and Julie joined eight other professional teams participating in the two-month Architectural Ceramics Assemblies Workshop. The other teams included:
- Eric Parry Architects + FMDC Ltd.
- ZGF + LERA
- Pickard Chilton + Magnusson Klemencic Associates
- Rios + ARUP
- HGA + Studio NYL
- Henning Larsen + Thornton Tomasetti
- Selldorf Architects + Socotec
The workshop immersed designers in all aspects of the terracotta design and fabrication process, giving them hands-on experience in pushing the boundaries of architectural ceramics. After months of preparation, the teams met at Boston Valley Terra Cotta's Buffalo, New York factory for a week-long workshop. Guided by specialists from Boston Valley Terra Cotta, the teams designed and fabricated their custom pieces in a collaborative environment where knowledge sharing was encouraged. The workshop concludes with a three-day symposium where each team presented a prototype of their design.
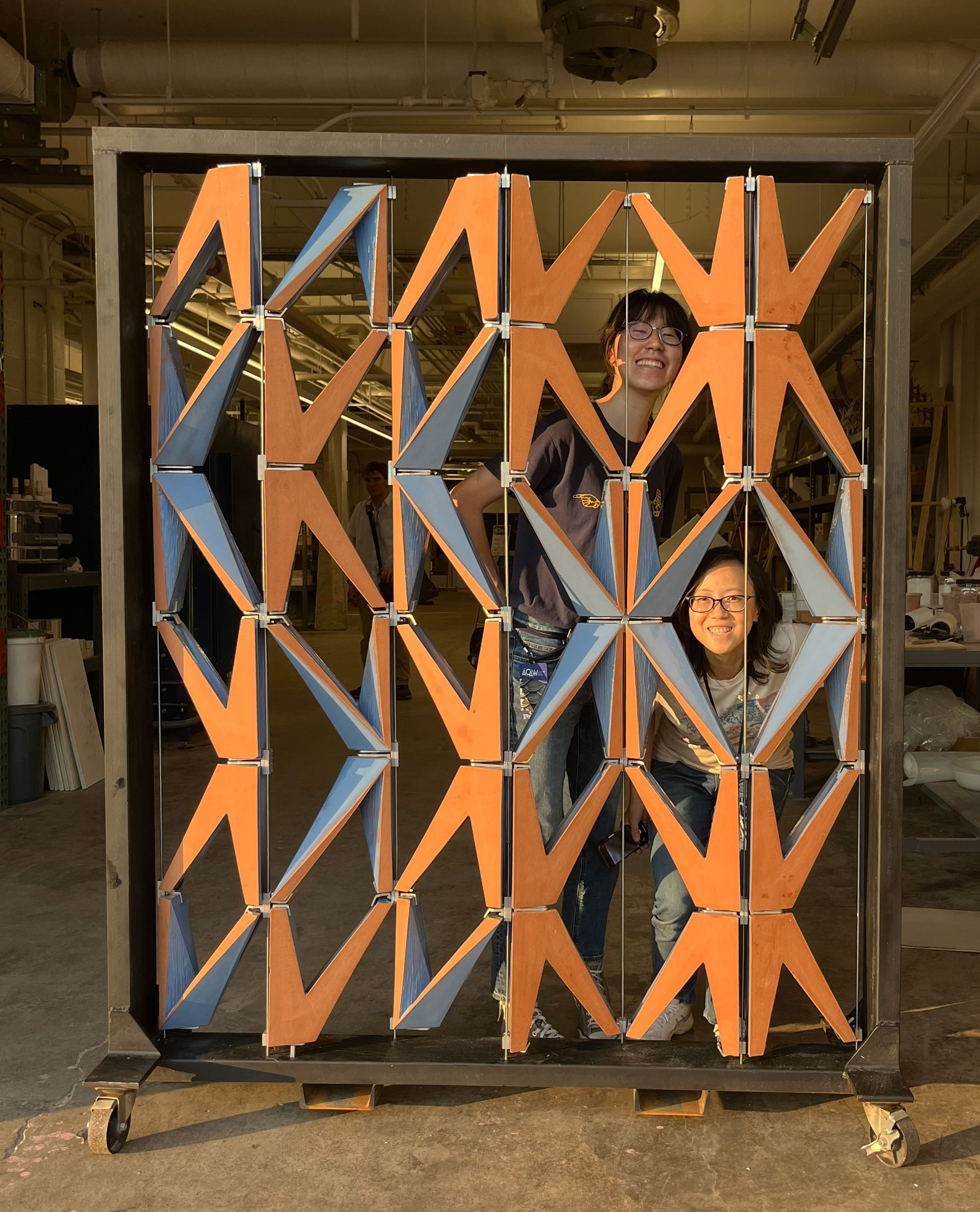
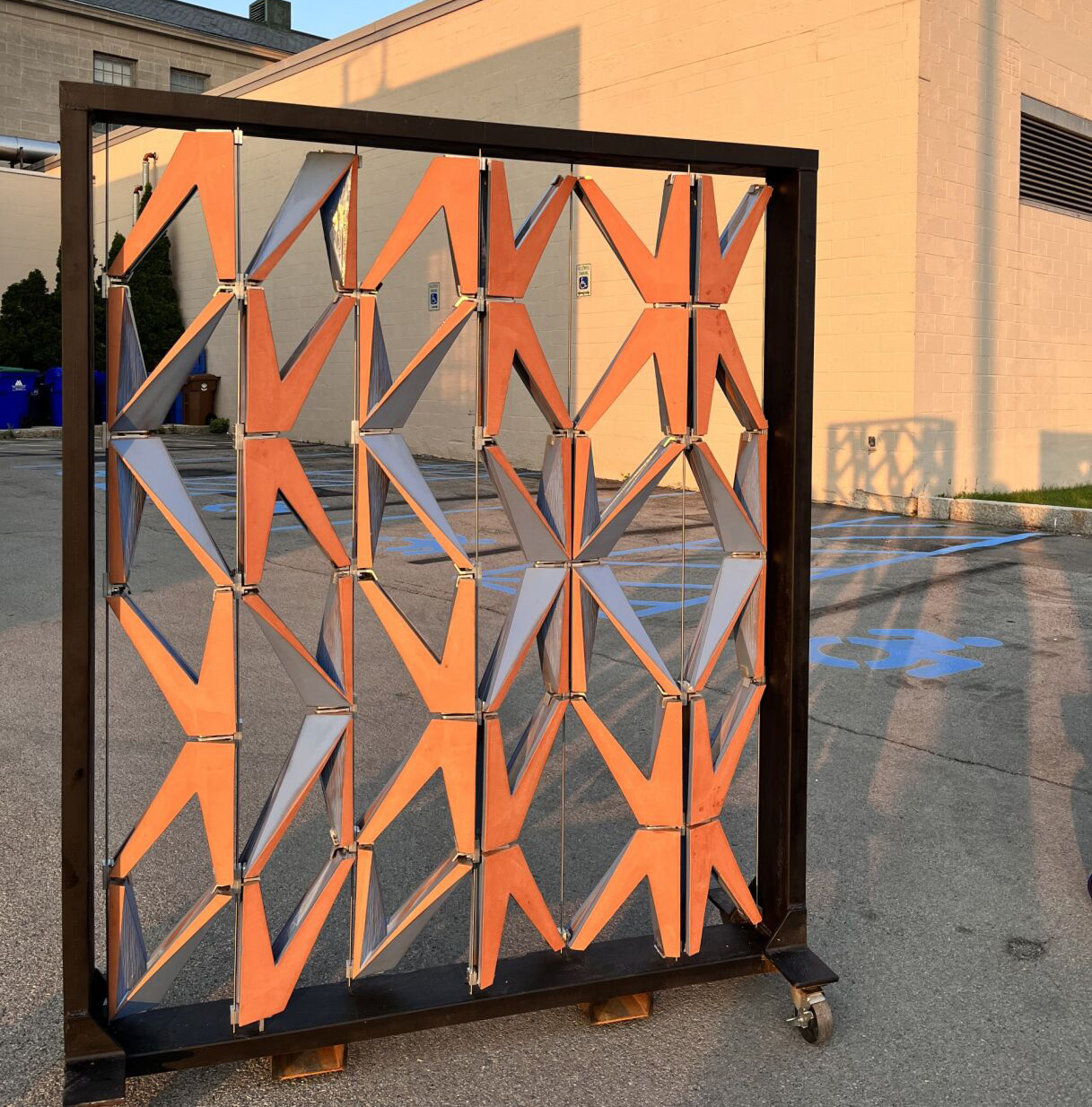
Ambiguity of Inside-Out
Our project challenges the way people experience terracotta. The idea was derived from our interest in how the materiality of terracotta can be fully expressed through the functionality of a screen shading system. The final module we created aims to provide a 360-degree viewing angle with the flexibility for different pattern arrangements. During our time participating in the ACAW workshop, we learned more about the constraints of fabrication, and explored ways to integrate texture and glazed and unglazed faces into the design. Our goal was to express terracotta's unique materiality and textures, as well as harness the effects of light on the material.
Design Inspiration
We started the design process by researching the different types of materiality that terracotta can achieve. We studied flower pots and rainscreen systems, which keep moisture out with glazed surfaces and retain moisture in the unglazed area. At the same time, we found repetition was largely used in the precedents we were studying. It is common to experience terracotta from only the front and back of the material. Our design challenged this by asking, how can we experience terracotta from all sides? This question led us to explore our design concept Ambiguity of Inside-Out.
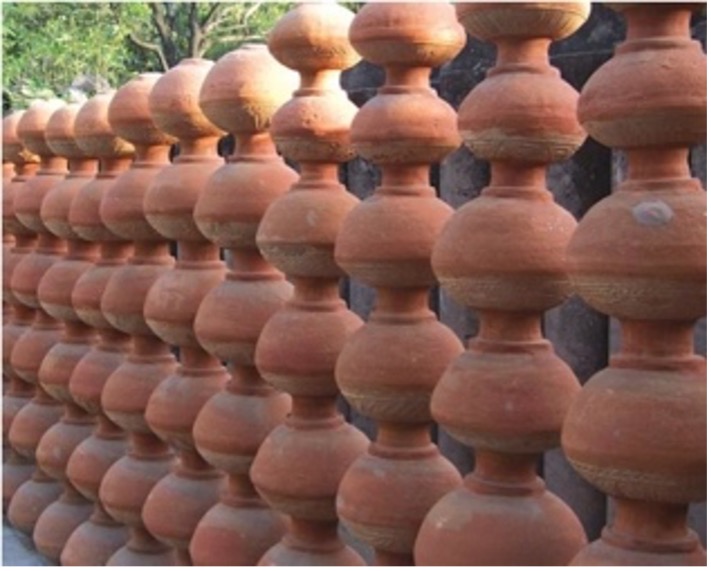
Terracotta Pots: Repetition, Materiality
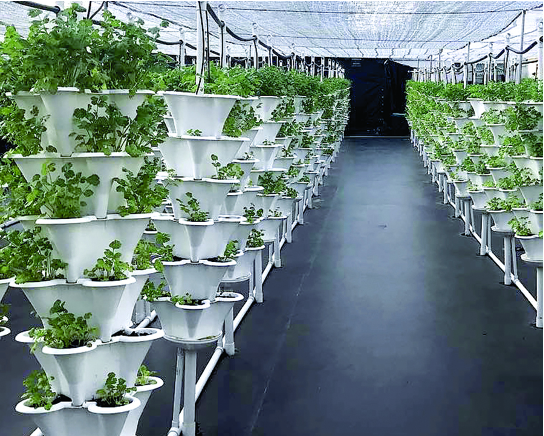
Vertical Garden: Planters, Green Walls, Programmed
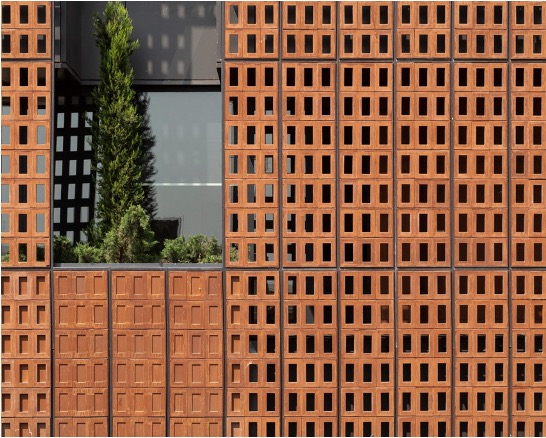
Screen Openings (Hooman Balazadeh): Module, 360 Degree
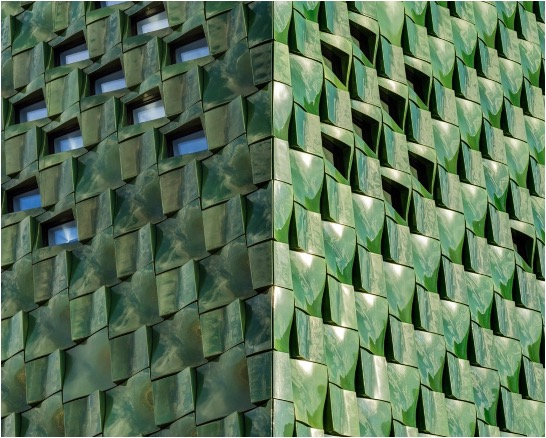
Ringling Museum (Machado Silvetti + Boston Valley): Glazing, Module
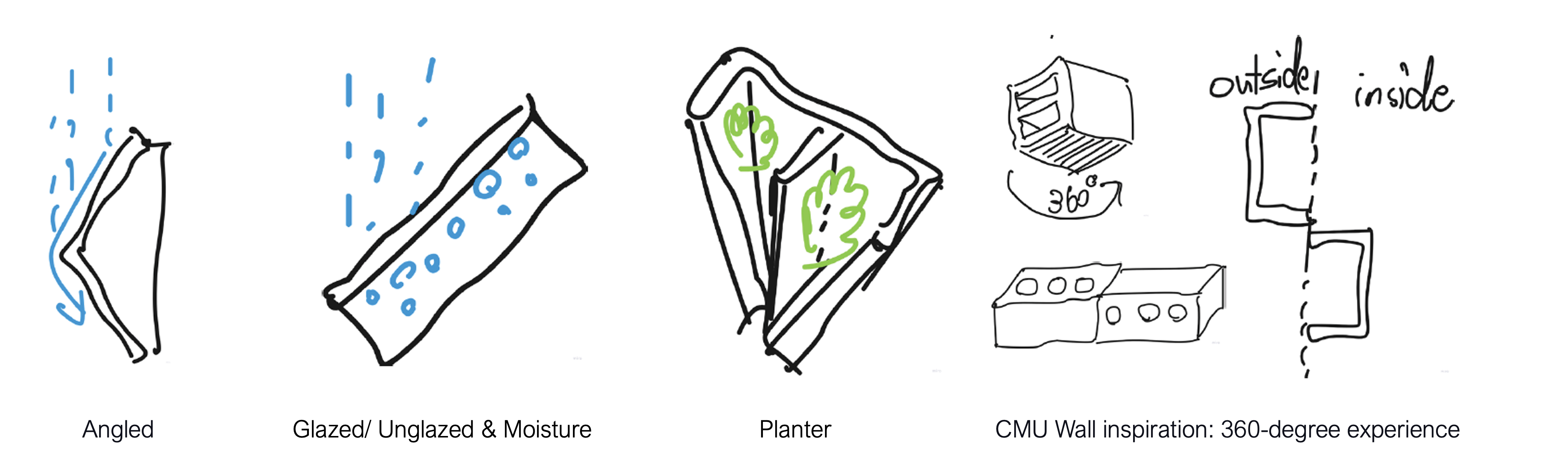
Concept
Our concept is a distinctive V-shaped facade system that is angled to direct water flow. It explores the natural characteristics of terracotta through glazed and unglazed applications and associates function with geometry and materiality.
Module Unit
The module unit was inspired by origami. We studied the effect of folding paper to create inward and outward surfaces. This allowed us to study a simplified geometry for a 360-degree experience. The rib directs and collects water, and has the potential to become a planter. Our design is flexible and can have glazed or unglazed faces to create a pattern that can be viewed from all the angles.
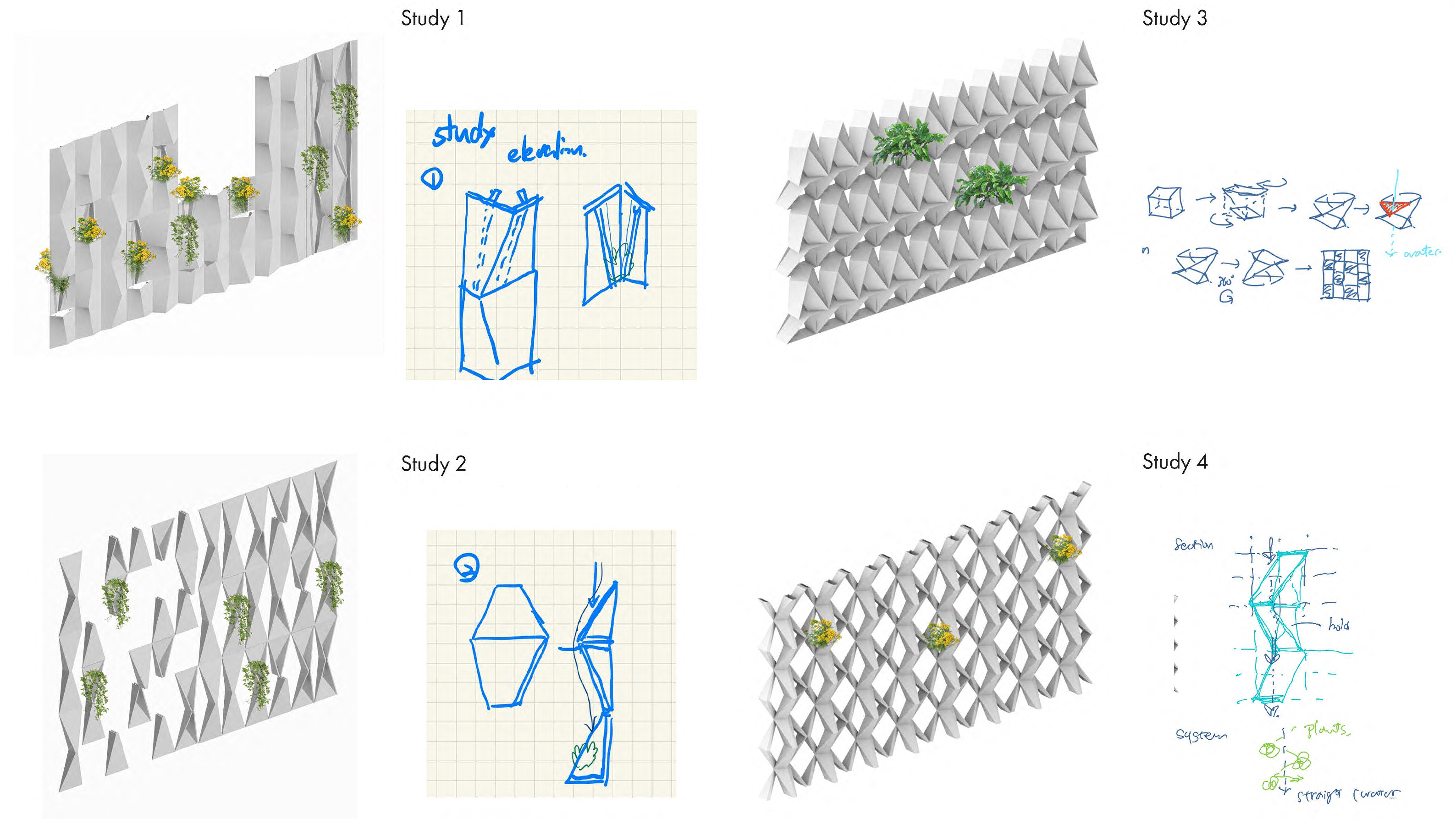
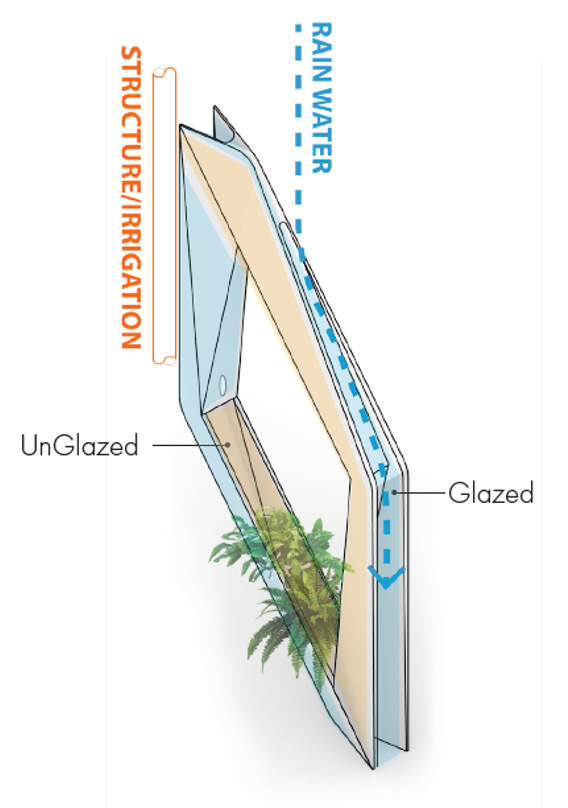
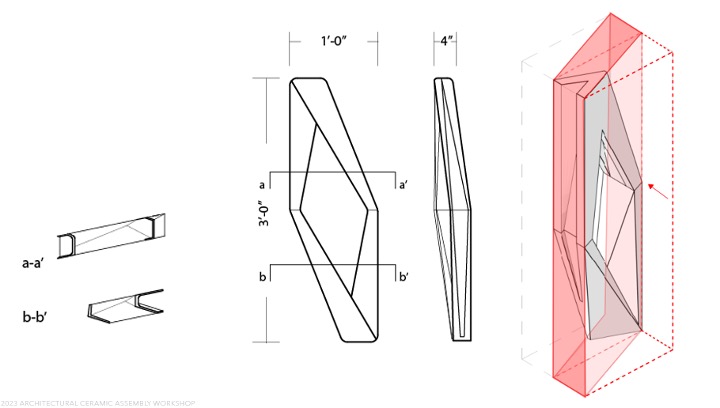
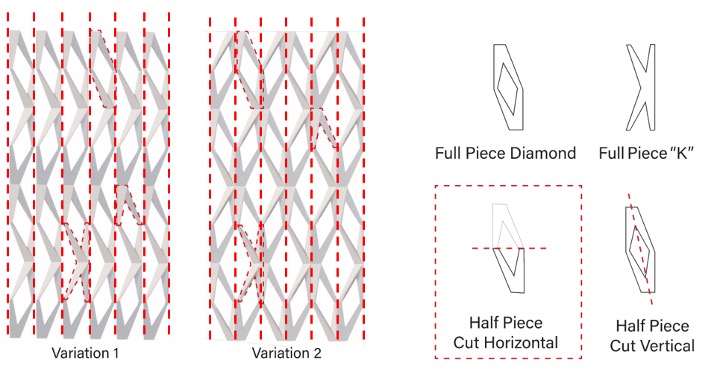
Configurations
The design allows for many different types of configurations and uses. It can be patterned in ways that could keep the quality of daylight. The variations can leverage the repetition capacity – slipping the geometry into two pieces instead of one diamond shape. Gradient colorization can be used to strengthen the read of the flow effects.
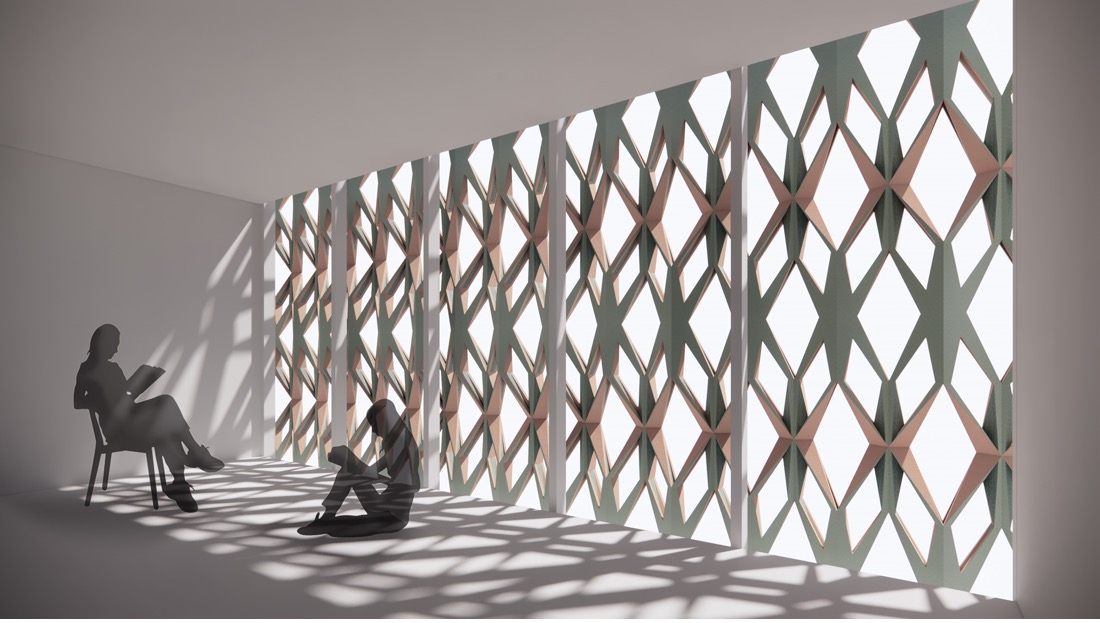
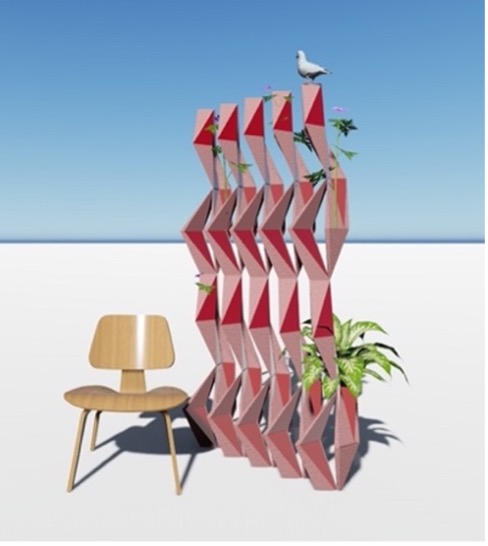
Textures
The contraction between terracotta and the glazing applied to it creates a compelling material experience. How can we create a textured glazing that emphasizes the feeling of flowing? “Flow” is the concept we had in mind from the starting point of our study on creating a water system for flower pots. We emphasized that the liquiform of glazing is like the flowing water by using score texture.
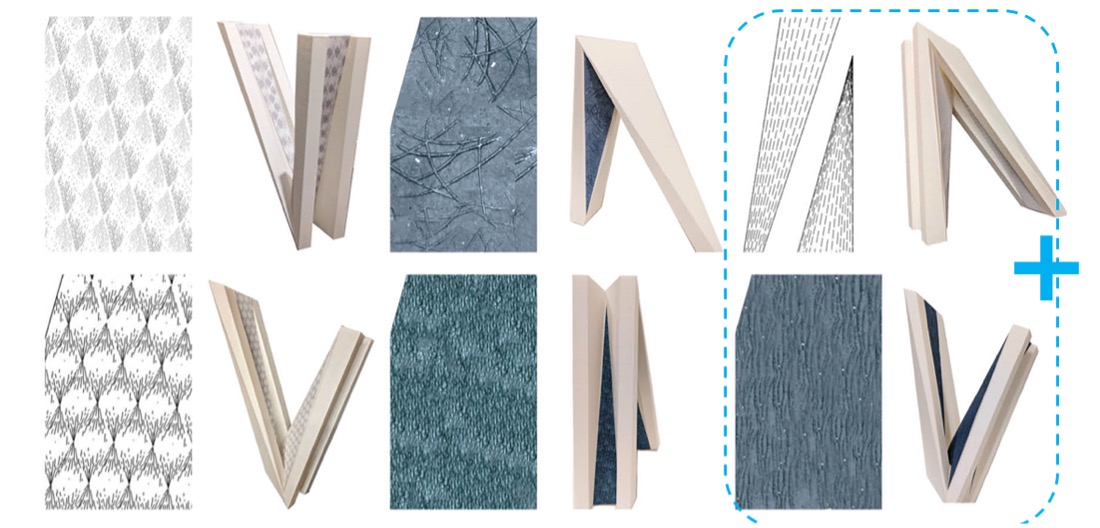
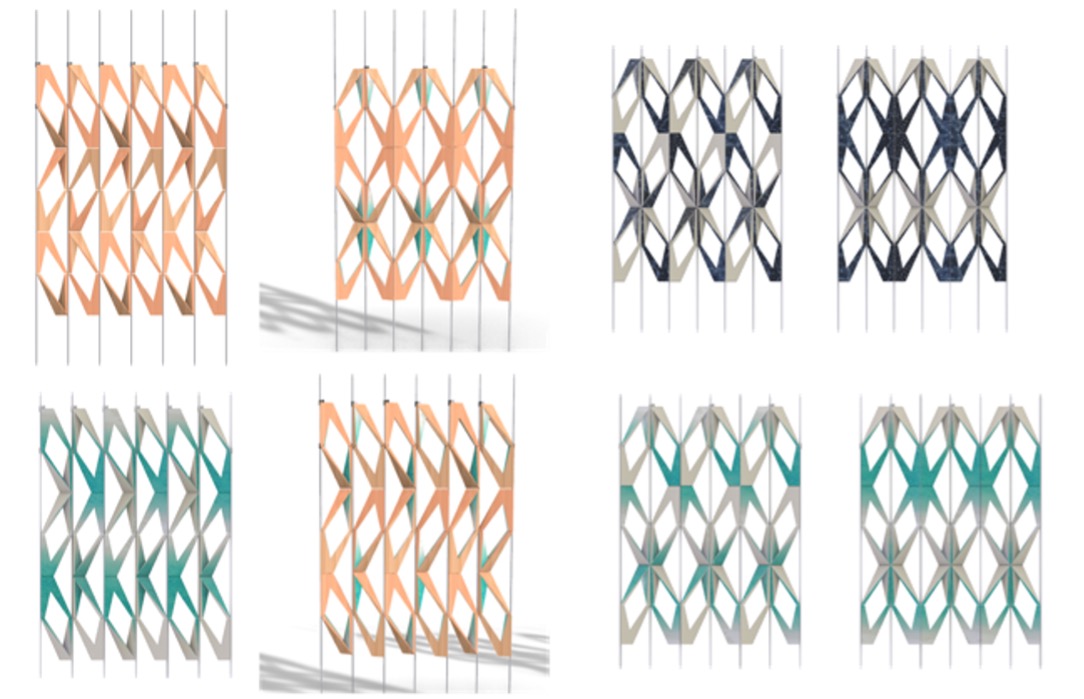
Variations
Our design leverages repetition capacity by slipping the geometry into two pieces instead of one diamond shape. Gradient colorization strengthens the read of the flow effects.
Glazing and Manufacturing
The final step was determining our manufacturing method. We chose slip casting over ram pressing as it maintained the channel geometry of the module best. We developed a slip-casting mold to understand which surfaces to apply textures to, and how these applications in mold can control the surface outcomes.
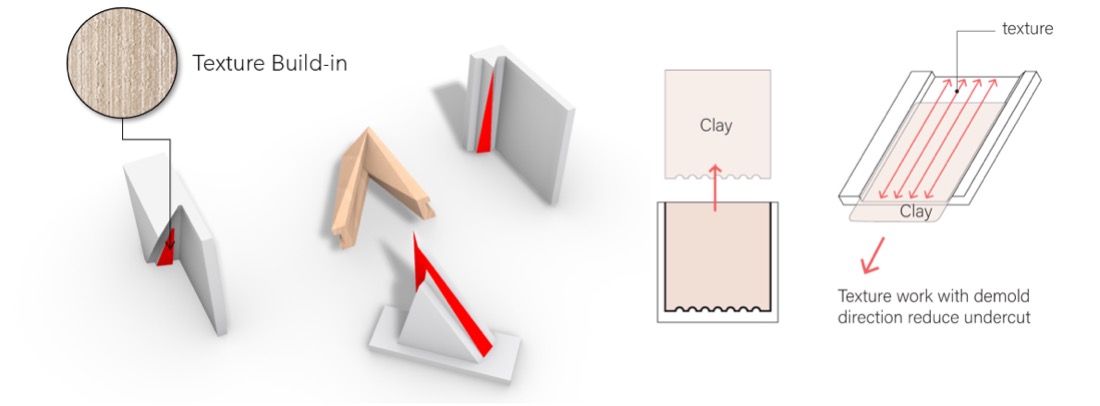
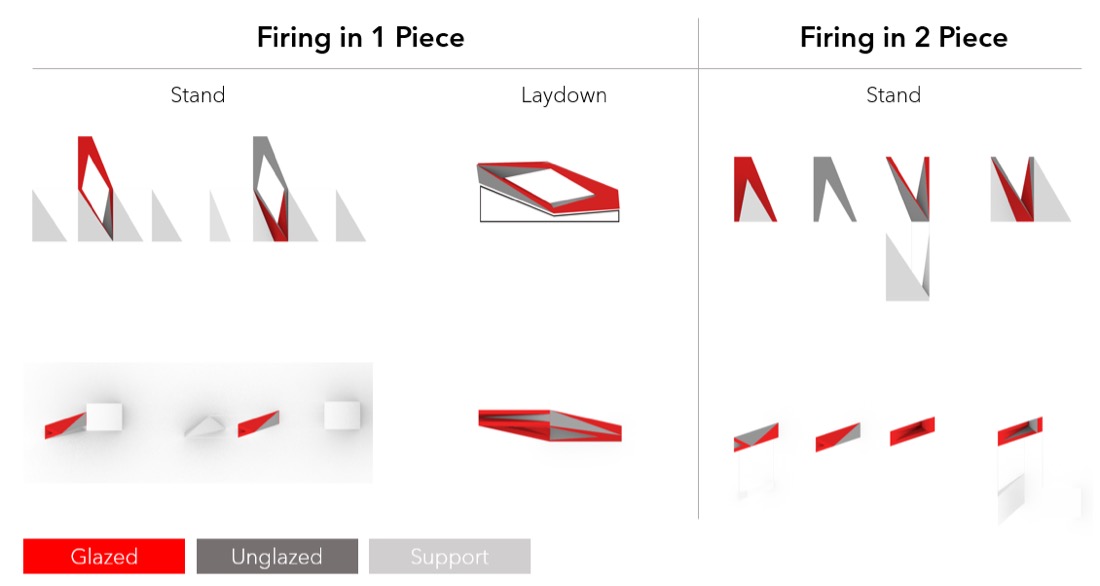
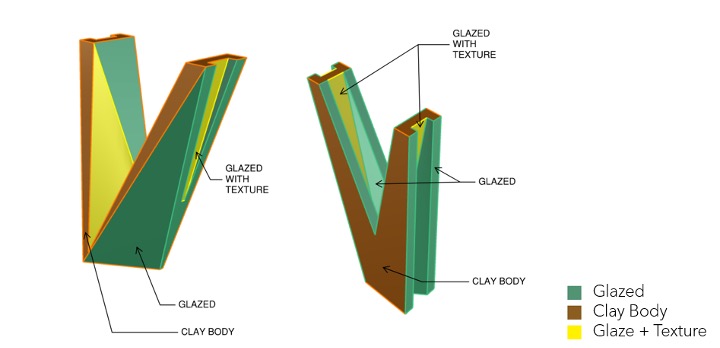
Glazing Process:
- The glaze was applied by brush and spray to cover all angles, but this caused uneven glaze display.
- After the first round of mockups, we agreed to reduce the glazing thickness to make the glaze show more clay body colors from the base of clay body.
Key Takeaways from the ACAW Workshop
We had an insightful and valuable experience participating in the Boston Valley Terra Cotta ACAW workshop! The process taught us many great lessons and helped us grow as designers. Some highlights of what we learned include:
- The importance of mockups. We have a better understanding of the materiality of terracotta from creating mockups. Although we know the percentage that terracotta might shrink, in the real world, it is still hard to predict. Testing and mockups are extremely important to understanding how the terracotta might perform.
- Communication is key. We learned to think about communication in a creative way so we were on the same page with the Boston Valley expert we worked with closely. We found that sometimes making is more effective than drawing, and sometimes you have to use the combination of both.
- The assembly process taught us to design with tolerance, and work with flexibility when material tolerance is not as expected.